0.866142mm; Precision is crucial in the fields of design and manufacturing, not just important. Even the smallest detail can have a big impact on the finished product. Though they may sound abstract, concepts like tolerances and specifications are essential to making sure that components fit together perfectly and perform as intended. 0.866142mm is one number that aptly demonstrates this idea; although it may appear arbitrary, this number has significant bearing on the manufacturing industry.
Tolerances, the permissible limits of variation in a physical dimension, are vital in ensuring that components align perfectly and function optimally. A deep understanding of these tolerances is crucial for designers and engineers alike. Misjudging these can lead to costly errors and inefficiencies, affecting everything from the product’s performance to its aesthetic appeal.
As we delve into the significance of specifications, it becomes clear that they influence every aspect of design and production. Specifications define the precise requirements that a product must meet, ensuring that it not only fits well but also performs reliably. They affect both the functional aspects of a product and its overall design integrity.
Join us in exploring why the measurement of 0.866142mm matters in modern manufacturing. This exploration will offer valuable insights into how precision and attention to detail can enhance your design projects. Whether you are an experienced professional or a newcomer in the field, understanding these concepts will help you refine your craft and achieve greater success in your projects. Let’s embark on this journey to uncover how precision and specifications shape the future of design and manufacturing.
Key Considerations for Setting Tolerances and Specifications

Determining appropriate tolerances and specifications is a nuanced process that requires careful consideration of several factors. Understanding these elements is essential for ensuring that a design meets both functional and practical requirements.
Firstly, material properties play a significant role. Different materials respond differently to stress and wear, which impacts how tightly tolerances need to be set. For instance, metals may expand or contract with temperature changes, influencing their tolerance requirements.
Functionality is another crucial aspect. Components that require a precise fit will need tighter tolerances compared to those with less stringent requirements. The functional demands of a design directly affect how exacting the tolerances need to be.
Environmental conditions must also be considered. If a product is exposed to extreme temperatures or high humidity, these factors can alter how components interact. Adjustments to specifications may be necessary to accommodate these environmental challenges.
Cost implications are equally important. Achieving stricter tolerances often involves more complex and expensive manufacturing processes. Balancing precision with cost efficiency is essential for maintaining budgetary constraints without sacrificing quality.
Finally, it is imperative to comply with regulatory standards. Adherence to industry regulations guarantees safety and promotes market acceptance. Achieving safety and competitiveness in your design process requires that you comprehend and incorporate these standards into your process.
Navigating the Challenges of Tolerances and Specifications in Design
Working with tolerances and specifications often involves overcoming several significant challenges. One of the primary issues is the inherent variability in materials. Even minor fluctuations in material properties can lead to discrepancies that impact the final product’s performance and quality.
Effective communication among teams is another critical challenge. Misunderstandings regarding tolerance levels can lead to costly reworks or project delays. While clear and precise documentation is essential, it is not always given the priority it deserves, which can exacerbate these issues.
Achieving cost-precision balance is also a challenging endeavor. Tighter tolerances can result in higher manufacturing costs even though they can improve product quality. Achieving the ideal balance between controlling costs and producing high-quality work is a never-ending task for manufacturers and designers.
Time constraints further complicate the process. Under pressure to meet deadlines, designers might make hurried decisions without fully assessing their impact on overall performance and reliability. This can lead to compromises in quality that affect the final product.
Lastly, evolving regulatory standards add another layer of difficulty. Keeping up with changing compliance requirements while still meeting design objectives demands continuous attention and adaptability from all parties involved. Staying informed and flexible is crucial for navigating these shifting regulations effectively.
0.866142mm: The Essential Role of Tolerances and Specifications in Design Precision
In the world of design, tolerances and specifications serve as the foundation for achieving precision and functionality. These critical elements determine how well parts fit together, ensuring that assembly is smooth and the final product performs as intended. Without these guidelines, even the most groundbreaking designs may encounter significant issues.
For any project to be successful, accuracy is essential. Smaller than intended deviations from tolerances can cause serious issues in production, including expensive mistakes and inefficiencies. Designers and engineers guard against these risks by establishing precise tolerances, guaranteeing that products live up to high expectations for functionality and quality.
Additionally, well-defined tolerances and specifications facilitate effective communication across teams. Engineers, manufacturers, and quality control personnel all depend on these consistent standards to ensure that their goals are aligned and that the production process runs smoothly.
Safety is another crucial consideration. Accurate tolerances are essential for minimizing risks associated with potential malfunctions or accidents in machinery and consumer products. Proper adherence to these standards helps ensure that products are safe for use and reliable in performance.
In a competitive market, brands that maintain stringent adherence to precise specifications can stand out. Consistent quality and reliability build trust with consumers, who increasingly expect excellence in every purchase. By prioritizing tolerances and specifications, businesses not only enhance their product integrity but also strengthen their reputation in the marketplace.
0.866142mm: The Importance of Understanding Tolerance and Specification Standards in Design

In the realm of design, a thorough understanding of tolerance and specification standards is essential for creating components that fit together flawlessly and perform as expected. These standards provide the framework for achieving consistency and quality across various projects.
The International Organization for Standardization (ISO) sets a comprehensive range of global standards that are crucial for maintaining high design quality. ISO standards cover numerous aspects, including mechanical tolerances and geometric dimensioning, and adhering to these guidelines can significantly enhance the precision and functionality of your designs.
In North America, the American National Standards Institute (ANSI) often complements ISO guidelines with specific requirements tailored to local industries. ANSI standards offer additional detail and context that are essential for meeting regional expectations and ensuring compatibility with other industry practices.
The American Society of Mechanical Engineers (ASME) also provides valuable standards, particularly through their Y14 series. These standards focus on drawing practices and emphasize precision and clarity in technical documentation, which is crucial for effective communication among engineering teams.
By familiarizing yourself with these key standards, you can improve coordination across teams, minimize errors, and achieve better project outcomes. Understanding and applying these standards will help you design components that not only meet but exceed industry expectations, leading to more successful and reliable results.
0.866142mm Distinguishing Tolerances from Specifications: Key Concepts for Design Success
In the field of design and manufacturing, tolerances and specifications are often discussed together, yet they serve distinct and vital roles. Understanding these differences is crucial for achieving precision and quality in any project.
Specifications outline the precise requirements for a component, including details about materials, dimensions, and performance criteria. They act as a comprehensive guide, defining what a product should accomplish and how it should be constructed. Essentially, specifications serve as the detailed blueprint for achieving the desired outcome.
Tolerances, conversely, address the allowable variations from these specifications. They specify the range within which deviations are acceptable without affecting the component’s functionality. This flexibility is essential in real-world manufacturing, where minor discrepancies are inevitable but must not compromise the product’s performance.
Understanding the differences between these ideas helps designers to establish realistic expectations and guarantees strict quality control throughout production. Engineers are able to successfully balance the needs for functionality and aesthetics, producing products that are dependable and of high quality, by developing precise specifications and acceptable tolerances.
Strategic Implementation of Tolerances and Specifications for Optimal Design
Effectively implementing tolerances and specifications demands a well-thought-out strategy. Begin by clearly defining your design requirements. This clarity will provide a solid foundation for all subsequent decisions and ensure that the design process remains focused and aligned with project goals.
Involve cross-functional teams right away. In order to guarantee a thorough comprehension of the specified tolerances, cooperation between designers, engineers, and manufacturers is imperative. All stakeholders benefit from early involvement as it helps to align their goals and resolve potential problems before they become apparent.
Leverage advanced software tools for tolerance analysis. These tools are invaluable for visualizing how variations in tolerances can impact the overall design integrity. By simulating different scenarios, you can identify and address potential problems before they affect the final product.
Regularly review and update your knowledge of industry standards relevant to your project. Staying informed about the latest best practices and regulatory requirements helps maintain high-quality outcomes and ensures compliance with current standards.
Meticulously document all decisions related to tolerances and their rationales. Comprehensive records not only facilitate future reference and audits but also provide a clear trail of the design choices made throughout the project. This level of documentation supports transparency and accountability in the design and manufacturing process.
Real-World Case Studies Highlighting the Critical Role of 0.866142mm in Design and Manufacturing
Case studies vividly demonstrate the critical role of the 0.866142mm dimension in design and manufacturing. One notable example involves a leading automotive manufacturer that struggled with component fit during assembly. Initially, their designs did not fully account for the tolerances associated with the 866142mm specification. After reassessing their approach and implementing more precise tolerances, the company achieved a remarkable 25% improvement in assembly efficiency.
In the aerospace sector, where precision is crucial, another company used 0.866142mm as a key reference in their design process for aircraft components. By adhering to stringent specification standards tied to this measurement, they were able to reduce component weight while enhancing structural integrity. This precision not only improved the overall performance but also led to significant fuel savings.
These case studies underscore the importance of understanding and applying precise tolerances and specifications. The impact of adhering to dimensions like 0.866142mm extends beyond simple measurements; it directly affects product quality and efficiency across various industries. Recognizing and leveraging these elements empowers designers and engineers to create innovative solutions that meet rigorous engineering standards and market demands, ultimately leading to better performance and reliability in their products.
The Crucial Role of 0.866142mm in Design and Manufacturing: Insights from Industry Case Studies
Case studies vividly illustrate the crucial role of the 866142mm dimension in both design and manufacturing processes. For instance, a well-known automotive manufacturer encountered difficulties with component fitting during assembly due to not fully accounting for the tolerances associated with the 0.866142mm specification. By revisiting their design strategy and adopting more precise tolerances, they significantly enhanced assembly efficiency by over 25%.
In the aerospace sector, where accuracy is critical, a company developing aircraft components used 866142mm as a fundamental reference point in their design process. Adhering to stringent specification standards related to this measurement allowed them to reduce component weight while ensuring optimal structural integrity, resulting in notable fuel savings.
These examples underscore the importance of understanding and applying precise tolerances and specifications. The influence of dimensions like 866142mm extends well beyond mere numerical values; they play a pivotal role in shaping product design and ensuring quality at every stage of production. By recognizing the significance of these elements, designers and engineers can drive innovation and meet both market demands and engineering standards more effectively.\
The Impact of Precision Measurements: The Role of 0.866142mm in Manufacturing
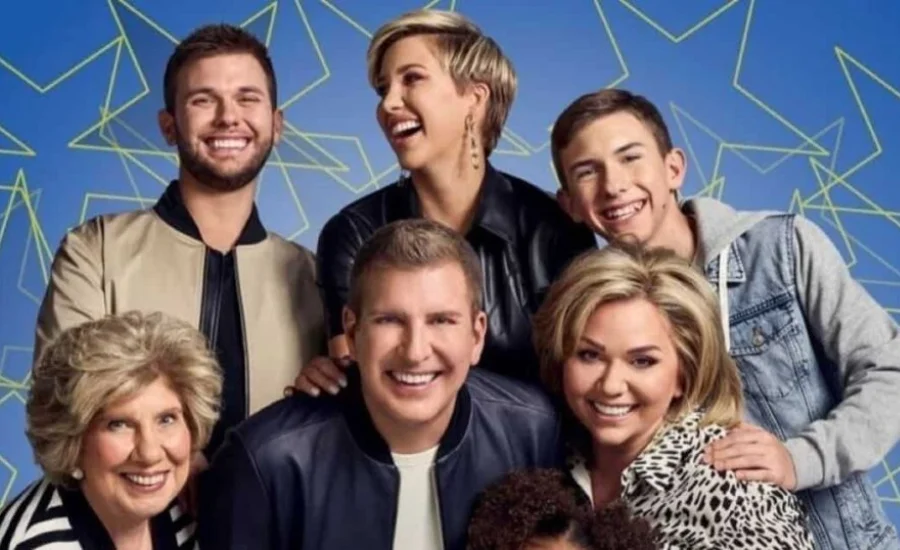
The dimension of 866142mm holds significant importance in the manufacturing industry, serving as a critical benchmark for maintaining precision throughout the production process. By adhering to this specific measurement, designers and engineers can ensure that components align correctly, which is essential for achieving seamless integration across various parts.
Incorporating this precise measurement into production processes helps minimize waste and enhances operational efficiency. When components are manufactured to meet this exact standard, it streamlines workflows and reduces the likelihood of errors during assembly, leading to a smoother and more effective production cycle.
Moreover, standardizing on such specific measurements improves communication among team members. Clear and consistent specifications ensure that all parties involved—designers, engineers, and manufacturers—understand the exact requirements necessary for successful project execution.
Companies that focus on precise tolerances, like 0.866142mm, often see significant improvements in product quality. High-quality outputs not only enhance customer satisfaction but also foster greater loyalty over time. Embracing exact measurements allows manufacturers to innovate while maintaining reliability and performance, ultimately supporting both creative and technical advancements in their designs.
0.866142mm: Key Considerations for Setting Tolerances and Specifications
It is a complex process that calls for careful consideration of a number of factors in order to determine the proper tolerances and specifications. To make sure that a design satisfies both functional and practical requirements, it is imperative to comprehend these components.
Firstly, material properties play a significant role. Different materials respond differently to stress and wear, which impacts how tightly tolerances need to be set. For instance, metals may expand or contract with temperature changes, influencing their tolerance requirements.
Functionality is another crucial aspect. Components that require a precise fit will need tighter tolerances compared to those with less stringent requirements. The functional demands of a design directly affect how exacting the tolerances need to be.
Environmental conditions must also be considered. If a product is exposed to extreme temperatures or high humidity, these factors can alter how components interact. Adjustments to specifications may be necessary to accommodate these environmental challenges.
Cost implications are equally important. Achieving stricter tolerances often involves more complex and expensive manufacturing processes. Balancing precision with cost efficiency is essential for maintaining budgetary constraints without sacrificing quality.
Finally, it is imperative to comply with regulatory standards. Adherence to industry regulations guarantees safety and promotes market acceptance. Achieving safety and competitiveness in your design process requires that you comprehend and incorporate these standards into your process.
Final Words
The seemingly abstract concept of tolerances and specifications, exemplified by the dimension 0.866142mm, holds profound significance in ensuring that components fit together seamlessly and perform optimally. These measurements, while they might appear as just numbers, have a substantial impact on the efficiency, quality, and overall success of manufacturing processes.
Understanding and applying precise tolerances like 0.866142mm can lead to substantial improvements in efficiency and product quality, as demonstrated by case studies in the automotive and aerospace industries. These examples highlight how meticulous adherence to specifications can enhance component fit, reduce waste, and lead to significant performance gains.
For designers and engineers, the challenge lies in navigating the complex interplay of material properties, functionality, environmental conditions, and cost implications while maintaining adherence to rigorous standards. By integrating precise measurements into their processes and leveraging industry standards, professionals can achieve high-quality outcomes and innovate without compromising reliability.
For more information join us on Celebz Wave